- Transformer Aluminium Strip
- Color Coated Aluminium Strip
- Aluminium Jacketing Insulation Coil
- PCB Entry Aluminium Board Strip
- Aluminum Plastic Composite Strip
- Aluminium Slit Strip
- Window Shutter Aluminium Strip
- Aluminium Corner Strip
- Aluminium Air Duct Strip
- Car License Aluminium Strip
- Heat Exchange Aluminium Strip
NEWS
INFORMATIONTel:
86 17344894490How to do the Aluminum plate extruded surface bubbly foaming
Last Updated :2023/07/03
How to do the Aluminum plate extruded surface bubbly foaming ?
In the extrusion process of the aluminum plate, the surface of the skin or air bubbles can appear. What is the cause? What method should be used to eliminate it?
What is a bubble or peeling: a convex bubble on the surface of the product, often seen in the head, tail, and the whole bubble, which has been cracked and called the skin.
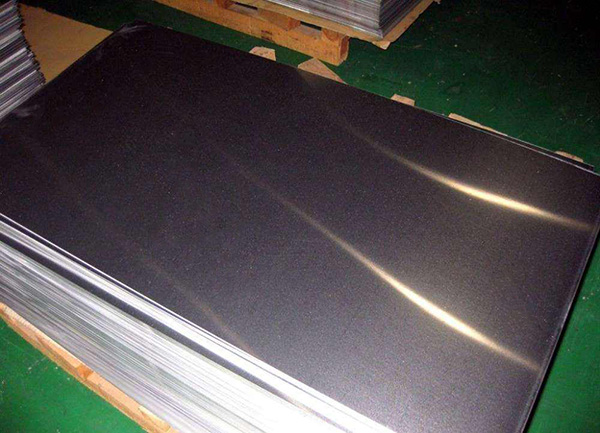
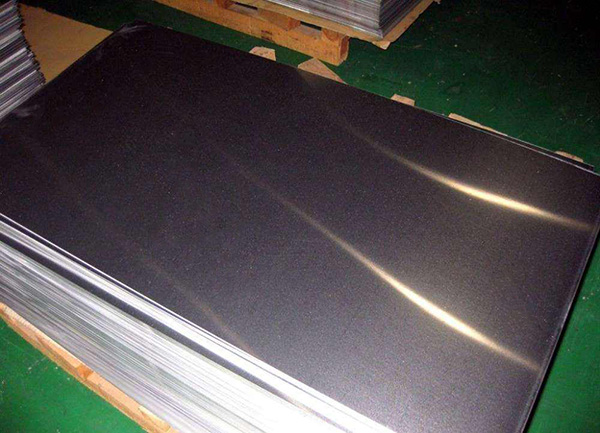
一. The cause of bubble and peeling of aluminum plate extrusion
1. The wear of extruded cylinder and extrusion pad is too poor, and the size of the extruded cylinder and the extrusion pad is improper, and the diameter of the gasket used is more than the allowable value;
2. The extruder and the extrusion pad are too dirty, with oil, water, graphite and so on;
3. The lubricating oil contains water;
4. The surface of casting is too much, too deep, or ingot surface has pores, sand eyes, loose tissue and oil, etc.
5. When replacing the alloy, it is not cleaned;
6. The temperature of the extruded cylinder and the extruded ingot are too hot;
7. The ingot temperature and size exceed allowable negative deviation;
8. The ingot is too long, the filling is too fast, the temperature of the ingot is not uniform, the non-drum filling is caused, so the exhaust is not complete, or improper operation, the discharge process is not carried out;
9. The die hole design is not reasonable, or the residual material is improper. The residual material in the shunt hole and the guide hole is partially brought out, and the air in the gap in the squeeze enters the surface.
二. The removal method of bubble and peeling of aluminum plate extrusion
1. Reasonable design of the matching size of extruded cylinder and extruded gasket, check the size of the tool frequently, ensure that it meets the requirements, and the extrusion tube should be repaired in a timely manner, and the extrusion pad cannot be too bad;
2. Tools and casting surfaces are kept clean, smooth and dry;
3. When replacing the alloy, thoroughly clean the cylinder;
4. Check the equipment and equipment frequently to prevent excessive temperature and speed;
5. Strictly implement process procedures and regulations;
6. The reasonable design, manufacturing mold, diversion hole and diversion hole design into 1 ° ~ 3 ° slope;
Strict operation, correct shear residue and complete exhaust.